As our understanding of diseases at the molecular level increases, so does the potential for monoclonal antibody (mAb) - related therapies. Platform approaches to mAb production, including purification, are a key to their successful manufacture and, in particular, streamline process development.
Monoclonal antibodies (mAbs) are approved for the treatment of a very wide variety of illnesses (Figure, May 2019. Download the pie chart for use in your own presentations).
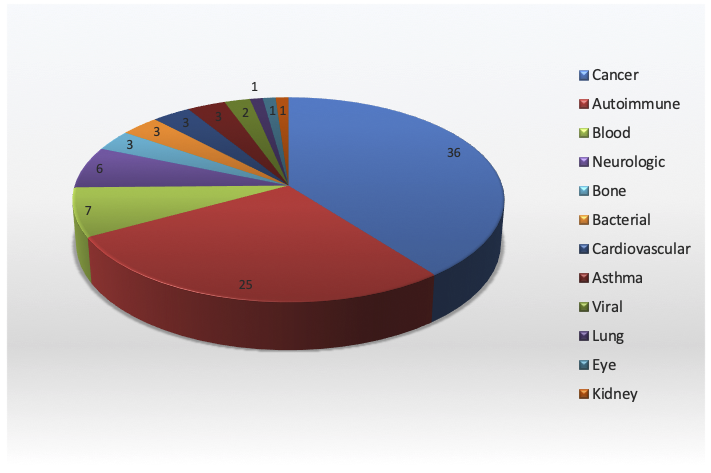
Those that are most successful, commercially, are directed against widespread disease categories. For example, Humira™ and Remicade™ are indicated for autoimmune illnesses such as rheumatoid arthritis, Crohn’s disease and plaque psoriasis, Avastin™ is used for colorectal and other cancers, Herceptin™ can treat breast cancer, and Xolair is used to treat asthma[1]. On the other hand, success can simply mean alleviating a disease which otherwise is untreatable, however rare.
MAbs are successful for several reasons, the most obvious of which is due to their high specificity for disease-related targets. As our knowledge of the molecular mechanisms of cancers and immune responses increases, so does the number of candidates for intervention at the molecular level. For example, in 2018 Nobel prizes were awarded to Tasuku Honjo and James Allison for their work on immune checkpoints: proteins that either stimulate or inhibit immune responses. Numerous recently introduced mAb therapeutics (such as Yervoy™, Opdivo™, Keytruda™, Tecentric™, Bavencio™, Imfinzi™, and Libtayo™) target these checkpoints. Furthermore, there are over 100 antibody immune checkpoint modulators in the development pipeline[2]. MAbs are often the most direct route to developing drugs that can interact specifically with such molecular targets.
Another factor in the success of mAbs is the standardization of production methods through the use of so-called platform technologies. This has resulted in the ability to produce large quantities of mAbs (thousands of Kg/year) to satisfy global needs for the so-called block-buster products, as well as enabling production methods for mAbs with narrower applications to be developed quickly and effectively. Standardized production methods reduce costs and guarantee rapid process development as new mAb candidates progress along the clinical pipeline. This is particularly important today when we see the number of candidate products increasing, for example due to numerous checkpoint modulators.
One of the cornerstones of mAb manufacturing is the use of Protein A resins in the purification process. Recent developments have resulted in higher binding capacities and improved life lengths, properties which have profound economic impact. At Bio-Works, we are making efforts on both fronts, as seen with the recent introduction of WorkBeads™ affimAb resin - an optimized alkali-stable Protein A resin designed for purification of mAbs, and WorkBeads 40 TREN - a multimodal AIEX resin used in flow-through mode to protect Protein A columns. Take a look if you are working on the mAb success story.
All product and company names marked with ™ are trademarks or registered trademarks of Bio-Works or of the respective trademark holders. Use by Bio-Works of trademarks of other holders does not imply any affiliation with or endorsement by them.
References
- The Increasingly Human and Profitable Monoclonal Antibody Market. Trends in Biotechnology (2019) 37:1, 9-16. António L. Grilo & A. Mantalaris. https://doi.org/10.1016/j.tibtech.2018.05.014
- Antibodies to watch in 2019. mAbs (2019) 11:2, 219-238. Hélène Kaplon & Janice M. Reichert. https://www.ncbi.nlm.nih.gov/pubmed/30516432